Electrical and Computer Engineering
Troy Fedderson, January 6, 2021
Steady engineering team docks successful U.S. Navy test
A well-prepared, student-led University of Nebraska–Lincoln Engineering team overcame unexpected challenges to secure a research victory that may help extend the life of U.S. Navy ships.
Through support from the U.S. Navy’s Office of Naval Research, the Nebraska team led by Yongfeng Lu, professor of electrical and computer engineering, has developed a laser-based system that prevents and repairs corrosion on aluminum-sided ships. Lu’s team has refined the laser system with optimized material processing parameters, making it portable, simpler and safer to operate — a combination that allows it to be used while at sea, granting ships an opportunity to operate longer and reduce frequent and lengthy dry dock repairs.
“We believe this to be a viable ‘shipyard on a ship’ concept,” Lu said. “It’s been exciting to see this science lead to engineering improvements and add value to the real world.”
Earlier this fall as part of a competitive bid process, Lu and his student-led team traveled (with permission and following COVID-19 protocols) to BAE Systems Norfolk Ship Repair in Norfolk, Virginia, to test the system while on a ship. The three-day opportunity was conducted alongside other teams, many from the private sector, and with officials from the Navy and Department of Defense observing.
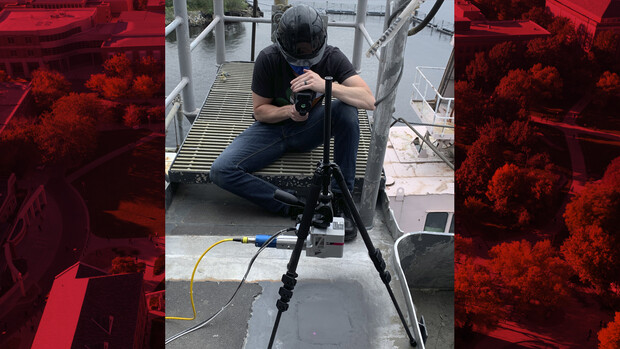
As the Nebraska team was setting up, a mistake damaged the optics system of the laser. A subsequent assessment of the damage led the team to one fix — they needed new components from their lab back in Lincoln.
“It was stressful, but we didn’t assign blame and concentrated on working together as a team, reviewing the damage and coming up with a necessary fix,” Tim Carlson, a third-year graduate student who helped lead the team, said. “We realized we needed new components shipped, so we reached out to team members back in Lincoln and they got the parts ready to go. That was day one.”
The parts arrived on the second day and, after a successful install and limited testing, the team was ready to get to work on day three. Carlson said the team calibrated the system and ran safety checks much of the morning before starting an actual test in the early afternoon.
“We were able to conduct three tests,” Carlson said. “With the first one, we ran into issues with paint within the scan area. Then, in the second test, we were unable to duplicate results at the level proved in the lab. That left us with one more opportunity to show that this system can be successful.”
As designed, aluminum-hulled ships are strong, but conditions at sea — primarily prolonged exposure to saltwater and sun — result in corrosion and hull cracks. To make repairs, crews must return to a shipyard, where damaged areas are replaced with new.
Lu’s Nebraska-developed system aims to reduce the time spent on dockside repairs. Through lasers, it treats aluminum alloys by heating a targeted area, a process that strengthens the microscopic boundaries between aluminum particles — an area more likely to corrode.
The system features pre-programmed recipes selected by entering details about the surface to be treated — from metal type to thickness. And, it has been designed to hang over the hull, operated by a small team while the ship remains in motion.
“We want our laser to work while a ship is in operation because it reduced time and cost,” Lu said. “We’ve also designed it to be simpler than using a cellphone, with just a few buttons to be pressed. That will help minimize the burden to the user.”
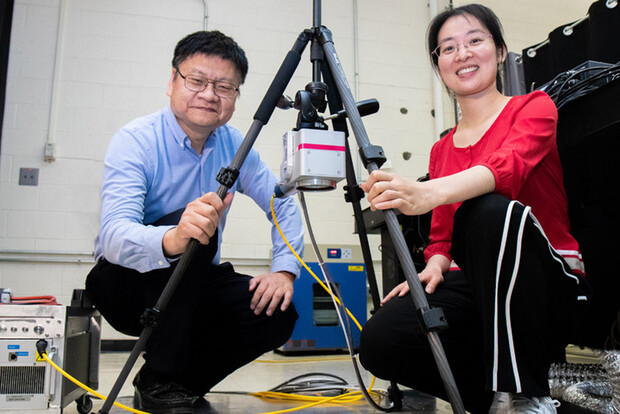
On average, aluminum alloys leaving a factory for use on ships have a sensitization level (a measurement that gauges susceptibility to corrosion or cracking) of around 15. Lower levels of sensitization are better with intermediate levels at 20 to 30 and high being more than 50.
In the lab, Lu’s team has shown that their device can draw steel at that 50+ level down to a three.
“That means our device can bring the hull back to a level that’s even better than factory aluminum alloys,” Carlson said.
In the third and final test on the Norfolk ship, the team duplicated results realized previously in pristine lab settings.
“We were on the ship, with lots of dust, noise and water — under pressure in a real-world environment, very different than a lab setting — and our team was able to prove the value of our system,” Lu said. “It was the perfect outcome for us.”
Lu also said he was impressed by the professionalism and flexibility of his team, working through equipment troubles and other issues to achieve an ideal result.
“I know they are a good team — I get to see that almost every day,” Lu said. “But this was very stressful and what was most impressive to me, though, was to see their calmness and determination in action.
“They showed they are Nebraska engineers, working together through a problem, overcoming obstacles and achieving success.”
The team has since continued refining the device, considering ways to make it lighter and easier to transport up steps within a ship. They are also working with NUtech Ventures, the university’s technology commercialization affiliate, to patent and further develop the system.
Members of Lu’s research team include Carlson, Nick Pease and Lei Liu.