Midwest Roadside Safety Facility
Scott Schrage, July 13, 2022
Barrier-connecting prototype shows prowess in crash tests
POCKET SCIENCE: EXPLORING THE ‘WHAT,’ ‘SO WHAT’ AND ‘NOW WHAT’ OF HUSKER RESEARCH
Welcome to Pocket Science: a glimpse at recent research from Husker scientists and engineers. For those who want to quickly learn the “What,” “So what” and “Now what” of Husker research.

What?
Highway drivers passing through construction zones may not give second or even first thought to the barriers that separate their vehicles from the workers on the other side of them. But those barriers — usually precast, portable segments of concrete — are often the only buffers protecting the construction workers from the tons of steel and aluminum sailing past them at roughly 50 miles per hour.
Any gaps between the segments of concrete barrier, whether a few inches or multiple feet, can compromise the safety of both workers and motorists. Unfortunately, overlapping the segments can eat up space that’s especially valuable when attempting to avoid bottlenecks by keeping adjacent lanes open to traffic. Prior designs aimed at covering up the gaps, meanwhile, have proven costly to install or difficult to transport around highway construction sites.
So what?
Nebraska’s Midwest Roadside Safety Facility and Department of Civil and Environmental Engineering decided to take on the problem, setting out to design, analyze and evaluate a crashworthy prototype that could span the gaps between portable concrete barriers. Ideally, the prototype would be simple to install and remove, adjustable enough to cover various sizes of gap, and constructed from standard, readily available components.
The team pared an initial round of seven designs to a pair, then put those two designs through the virtual rigors of computer simulations before selecting just one for high-speed crash testing. Across two crash tests, the engineers flung a 5,000-pound pickup truck toward critical points of a gap-covered barrier. In both cases, the team’s prototype helped the barrier maintain its structural integrity, protect a hypothetical driver and safely redirect the vehicle following impact.
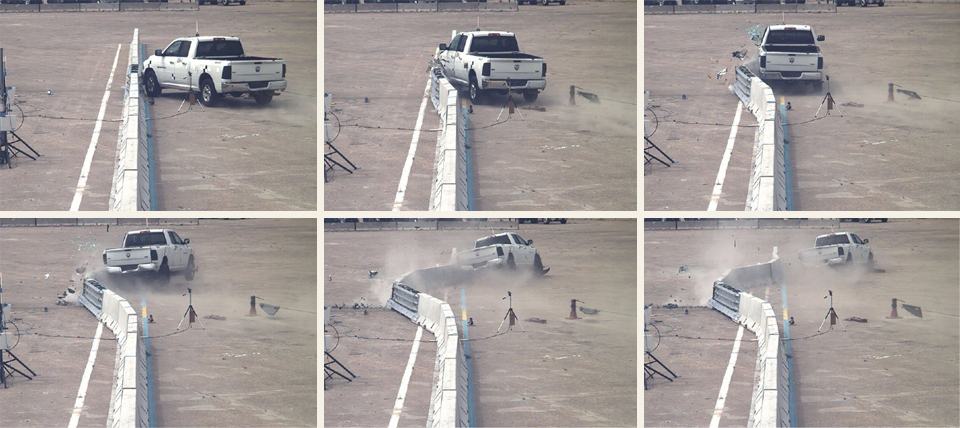
Post-crash analyses helped the team draft recommendations about how to calibrate the positioning and installation of the gap-spanning hardware, especially to accommodate various-sized gaps in the barrier.
Now what?
Having met the safety requirements set forth in federal guidelines, the hardware can now be applied to gaps ranging from 6 inches to 12.5 feet in a common type of concrete barrier. Employing the hardware in other, differently shaped barriers will require further analysis and testing, the team said.
